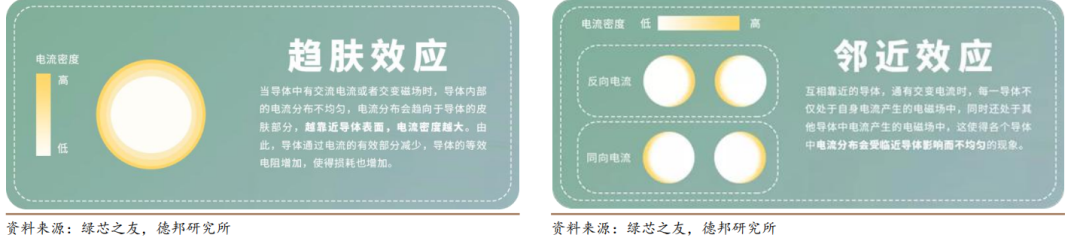
- 提高扁线的宽高比,间接增加扁线的比表面积;
- 减小导线尺寸,间接增加扁线的比表面积,但这同时也会降低槽满率,需要综合评估;
- 采用多档变速箱,降低电机转速,代表车型为保时捷Taycan;
- 3D打印铜线,导体尺寸和横截面可以任意变化,给了绕组设计极大的自由空间,该方案导致导体内的电分离结构,所述电分离结构用于限制涡流路径,因此电流密度被“强制”到剩余的导体横截面上,此外借助于3D打印可以实现任意连接的几何形状,不需要传统的绕组接头焊接工艺,该方案短期内无法实现量产。
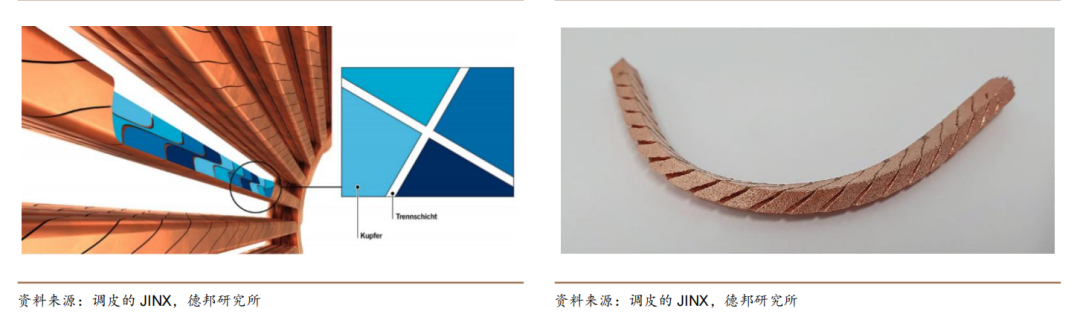
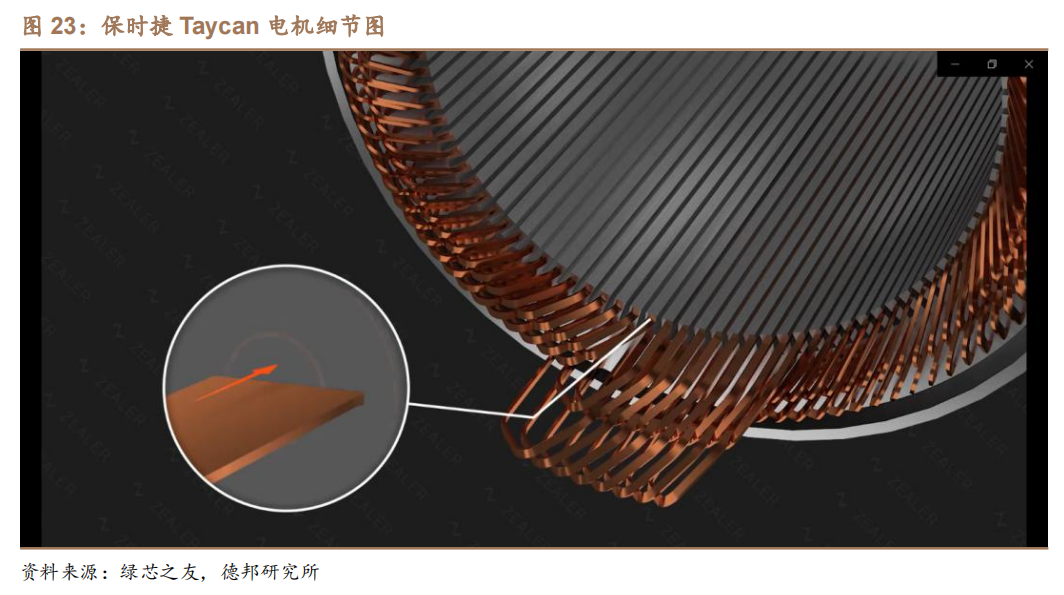
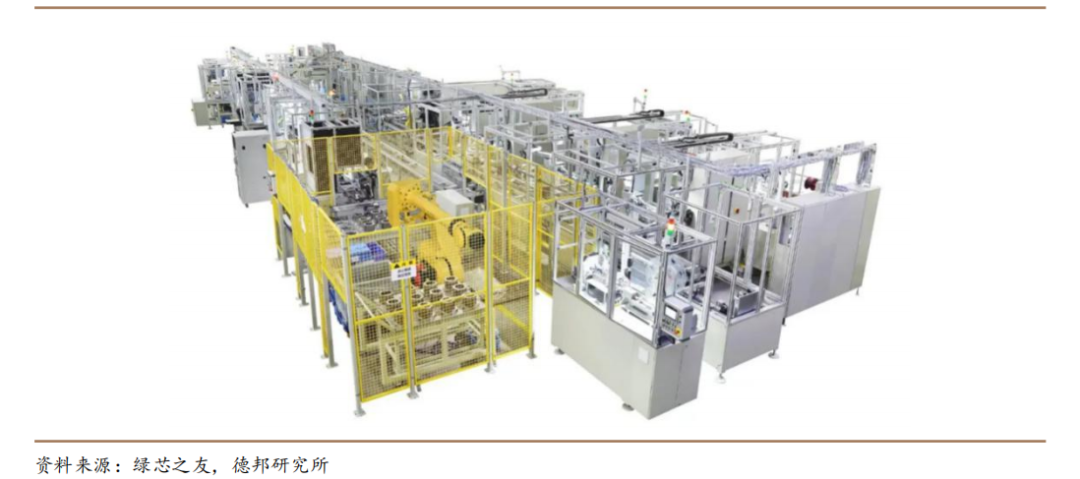
- 从圆形切换到矩形形状,导致铜线生产加工工艺更加复杂;
- 涂覆难度增大,扁平线R角处的漆膜涂覆非常困难,很难保证此处绝缘层的均匀性;绝缘涂层在烘干后会产生收缩,扁线是非均匀收缩,容易变形,需要改良使得R角处的涂覆厚度更厚;
- 扁线弯折成发卡后,R角处应力集中,容易导致涂覆层破损;
- 对扁线的精度要求高,扁线截面积大、匝数少,单根导线不一致对整体性能的影响显著增大,对扁线的一致性要求高,复杂的加工成本使得扁线成本更高,也使得扁线加工企业享受更高的技术溢价;
- 新能源汽车所使用的漆包线直接关系到整车运行稳定性,对电磁线厂家的质量控制流程、研发与工艺设计能力提出了很高的要求,需要对拉丝和包漆速度、拉丝与包漆的协调、拉丝模具配置、张力控制、涂漆模具配置、烘焙温度、绝缘漆粘度、工作环境等多个控制点的合理设计、严格控制。
扁线的最大成本是原材料无氧铜杆,加工费在电机中的价值量并不高。稳定地供给合格的产品是与车企合作的关键,在原材料是主要成本的情况下,车企寻求加工费更低的供应商的动力并不高。