1、热管的导热系数很少达到规格极限值
热管导热系数范围为10,000至100,000 W/mK。大约是铜的250倍,是铝的500倍。但是,与金属不同,热管的有效导热系数随热管长度变化很大。
图1显示了长度对热管导热系数的影响。在这个例子中,我们使用三根热管来传输75W的热量。虽然在不到100mm的热管长度下实现了10,000W/mK的导热率,但是200mm长度具有不到规格100,000 W/mK的最大导热率的三分之一。
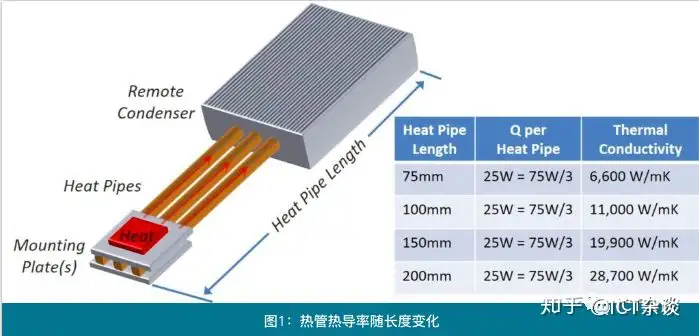
2、热管应用差异化比较大
热管的性能数据通常是典型状态下的,但实际应用场景却不相同。
打扁和折弯会对热管性能产生负面影响,但工艺上可以轻松实现,满足系统散热设计上的需求。
如果需要更低的热阻,则可以在加工热管时,形成能够与热源直接接触的光滑表面,从而消除、减少界面热阻。
如果需要直径从一端到另一端不同的热管,使蒸发器端部完全覆盖热源,而其余部分保持足够小。
热管内部结构的变化,尤其是毛细结构孔隙率和厚度,可以进行调节来满足特定的一些应用要求。例如,当需要给定直径的热管在较高功率负载或重力下操作时,毛细管压力就需要增加。对于更高的Qmax,这意味着更大的孔隙半径。为了有效地抵抗重力(蒸发器下方的冷凝器),这意味着更小的孔隙半径和/或增加的孔隙厚度。另外,可以沿着单个管的长度改变毛细结构的厚度和孔隙率。
3、结构形式影响热管性能
一旦确定了热管的内部结构,就能清楚外部物理特性如何影响性能。热管应用,尺寸通常最重要。但是,外观改变会也会降低性能。
打扁
图2显示了最常见的热管尺寸的性能(Qmax)。不同供应商的热管Qmx会不同。

图 2: 热管Qmax可定制
通常,烧结型热管可以被打扁至其原始直径的30-60%。有人认为,当打扁到直径的一半后,性能就会极具下降,实际上这并不正确。例如,VC就可以认为是一个超大的热管被打扁到90%以上。
对于热管应用有两个重要的性能限制:毛细结构和蒸汽腔。毛细限制是毛细结构将水从冷凝器输送回蒸发器的能力。如上所述,我们可以将毛细结构的孔隙率和厚度调整到特定情况,来改变Qmax和/或抵抗重力的能力。蒸汽腔极限是由蒸汽从蒸发器移动到冷凝器的空间有多大。
图3中的橙色和蓝色线描绘了图2中所示的各种热管尺寸的相应限制。 这两个极限中较小的一个决定了Qmax,并且如图所示,蒸汽腔极限高于毛细结构极限。随着热管扁平化,可用于蒸汽移动的横截面积逐渐减小,使得蒸汽腔极限向下移动。只要蒸汽腔极限高于毛细结构极限,Qmax就保持不变。
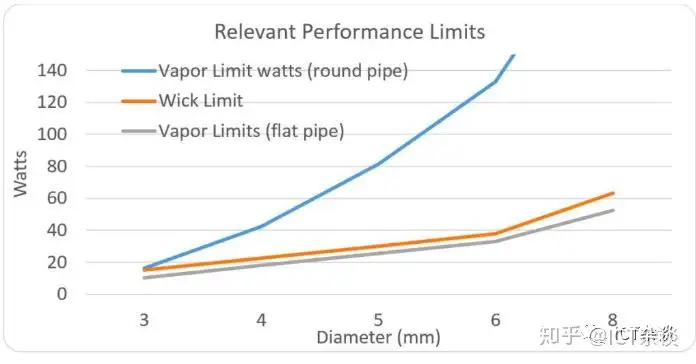
图3:热管性能极限
在这个例子中,我们选择将热管压扁到图2中的规格。如灰线所示,蒸汽腔极限低于毛细结构极限,降低了Qmax。将3毫米打扁仅仅33%就会导致蒸汽腔极限成为决定因素,但对于8毫米的热管打扁超过60%才能实现这一点。
折弯
折弯热管也会影响性能。这里提供一些经验法则。首先,最小弯曲半径是热管直径的3倍。其次,每一个45度弯曲将使Qmax降低约2.5%。从上面的图2可以看出,当打扁到2.5mm时,8mm的热管的Qmax为52W。将其弯曲90度将进一步减少5%。新的Qmax将是52-2.55 = 49.45瓦
抗重力
图4说明了蒸发器与冷凝器的相对位置如何影响Qmax和热管选择。在每种情况下,Qmax从一个方向极限到下一个方向极限减少了大约95%。
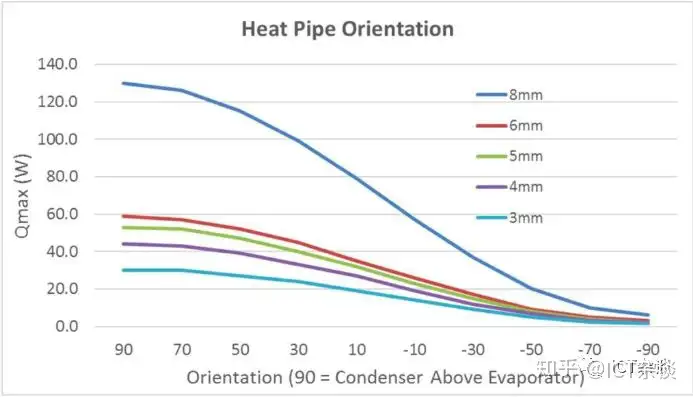
图4:方向对热管性能的影响
在冷凝器必须放置在蒸发器下方的情况下,我们将使用允许较小孔隙半径和/或增加毛细厚度的烧结型材料。例如,如果我们优化8mm热管以抵抗重力(-90 o),我们可以将其Qmax从6W提高到25W
4、热管设计举例
假设以下是已知的限制:尺寸为20×20mm的70W热源和将热量从蒸发器传递到冷凝器所需单个90度弯曲热管。
- 为了达到最最有效果,热管需要完全覆盖热源,在这种情况下,热源宽度为20毫米。从图2中可以看出,我们有两种选择:三个圆形6mm热管或两个扁平8mm热管。
- 热管可以联合使用。6mm热管Qmax为114W(3x38w),而扁平8mm热管的Qmax为104W(2x52w)
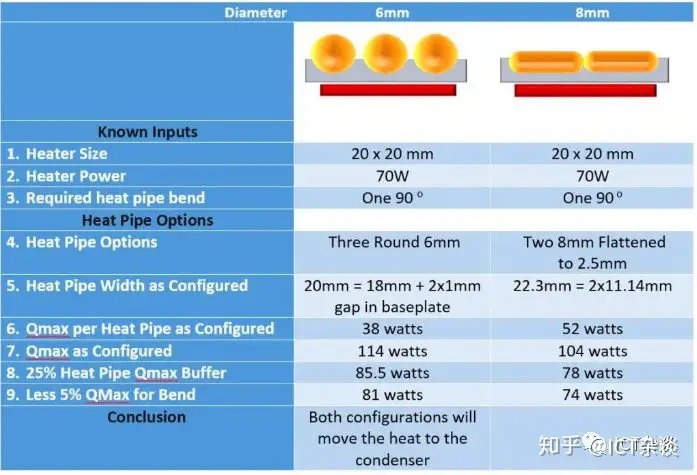
图5:热管配置选择
- 考虑一定的安全余量是良好设计的要求。设计时,依据最大性能的75%进行选择。因此,6mm(75%x 104W)为85.5W,8mm(75%x 104w)为78W
- 下一步需要考虑折弯。90度折弯将导致Qmax减少5%。6mm方案Qmax现变成81W,而对于8mm方案,为74W,两者都需要冷却的70W热源。
可以看出,两种热管设计方案足以将热量从蒸发器移动到冷凝器。那么为最终的选择决定性因素是什么呢?从结构设计角度来看,可以简单地归结为蒸发器处的散热器高度。8mm方案的轮廓比6mm方案低得多。相反,如果要提升冷凝器的效率则可以通过在三个位置而不是两个位置输入热量来提高,这种情况下就需要选择6mm方案。
如前文所述,本文并非是提供有关热管和散热器设计的详细培训,而是提供有关所用热管数量和尺寸的指导,并提供一些用于估计散热器尺寸并确定一些安装方法。散热器的类型从铝挤到机加、插翅有多种选择,每种都有自己的成本和性能特征。虽然散热器的选择显著影响散热性能,但任何类型的散热器最大性能提升都和强迫对流相关。
下图对各种形式的散热器进行了总结,分别从成本、有点、潜在缺陷三方面进行了分析。
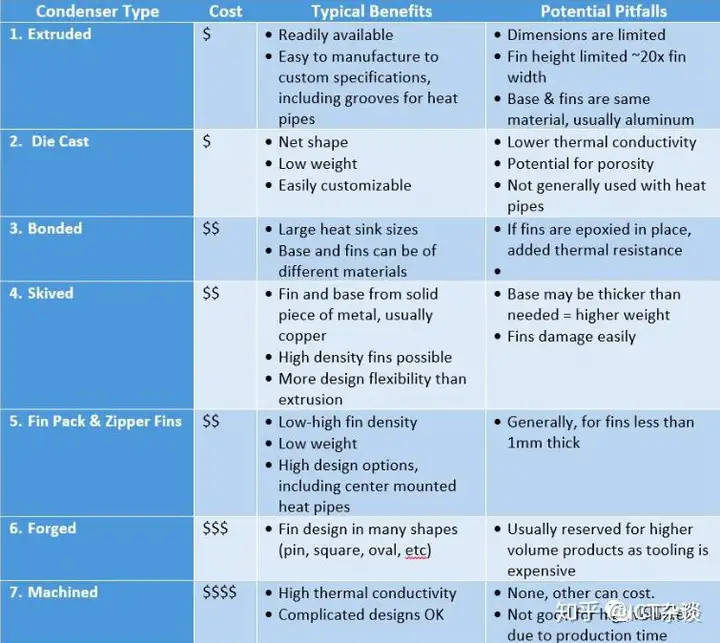
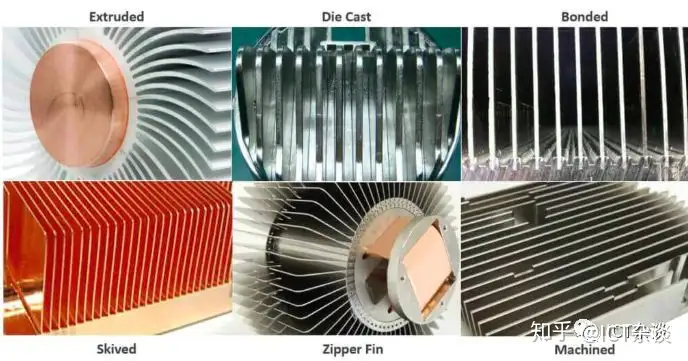
图6:散热器类型择
估算所需的散热器体积可以通过使用下面的简单公式,我们可以估算冷却热源所需的散热器的总体积。V =(Q * Rv)/ △T 体积是散热器的外部尺寸。Q是以W为单位的功耗,Rv是体积热阻(cm 3 -C / W)。图7 在不同的流速下的一些热阻值。首先要注意的是强迫对流对热性能的影响巨大。即使气流速度很小,散热器的体积热阻也减少了三分之二。
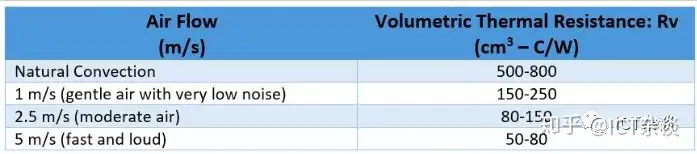
图7:流速和体积热阻的关系
假设我们有一个50W的热源Q,它的最大工作结温度(Tjunction)是100℃。减去最大允许的环境温度电子温度,得到:
△T:在这个例子中是100 – 70 = 30 ℃
如果我们设计一个电脑,我们可能会是一个半或完全密封的外壳,也就意味着我们是自然对流散热器。
由此散热器体积将是:V = (50*500)/30= 833cm³ ,相当于一个9.4 x 9.4 x 9.4厘米。
显然,在自然对流环境中,我们不会用一个9.4厘米高的散热器,所以长度和宽度的尺寸必须大幅增加。但是,我们可能会猜测,这个应用可能需要使用底盘盖作为散热器。有一个这样的应用的例子,它的热负荷、环境工作温度和无风扇设计都与上面的例子相匹配。让我们看看设计的下半部分。PCB的底部包含大约50W的处理器和芯片。铜基板尺寸是25cm×15cm。同时总厚度是7.5cm,总体积为938cm³ 。
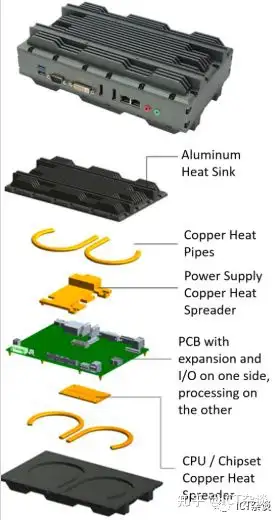
图8:某案例
如果使用强迫风冷,所需的散热器体积将减少多达十倍。散热器设计的下一步将是详细建模,然后进行CFD分析。这将使工程师充分了解最优的基础厚度,翅片间距,翅片高度,和基板/翅片材料等。
无论系统是局部还是远端热源,将热管与冷凝器设计匹配的要求都是相同的。基板开槽除外,简单地将圆管焊接到平面上是肯定不好的。圆形或半圆形槽应挤压或和散热器加工成一体。为了给焊料留出足够的空间,建议将凹槽的尺寸比热管的直径大0.1mm左右。图9中的散热器同时使用近端和远端散热器。挤压式设计是为了适应扁平热管,最大限度地增加铜基板和热源之间的接触。一个远端冲压翅片散热器可以进一步提高热性能。这种设计作用很大,因为这些管道可以直接穿过翅片中心,减少翅片长度上的传导损失。同时这种翅片不需要基板,重量和成本都可以降低。同样,安装热管的孔应该比热管直径大0.1mm。如果管道在热源处完全是圆的,基板厚度要增大,如图10所示。
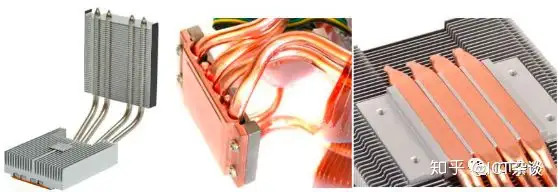
图9:热管沟槽安装 图10:热管块固定 图11:热管直接压接
如果基板和额外的界面材料造成的传导损失仍然对于散热有影响,则可以通过工艺保障平整度,让热管和热源直接接触,如图11所示。这种结构通常会使温升降低2-8℃。如果需要热源与热管直接接触,则应考虑采用VC。