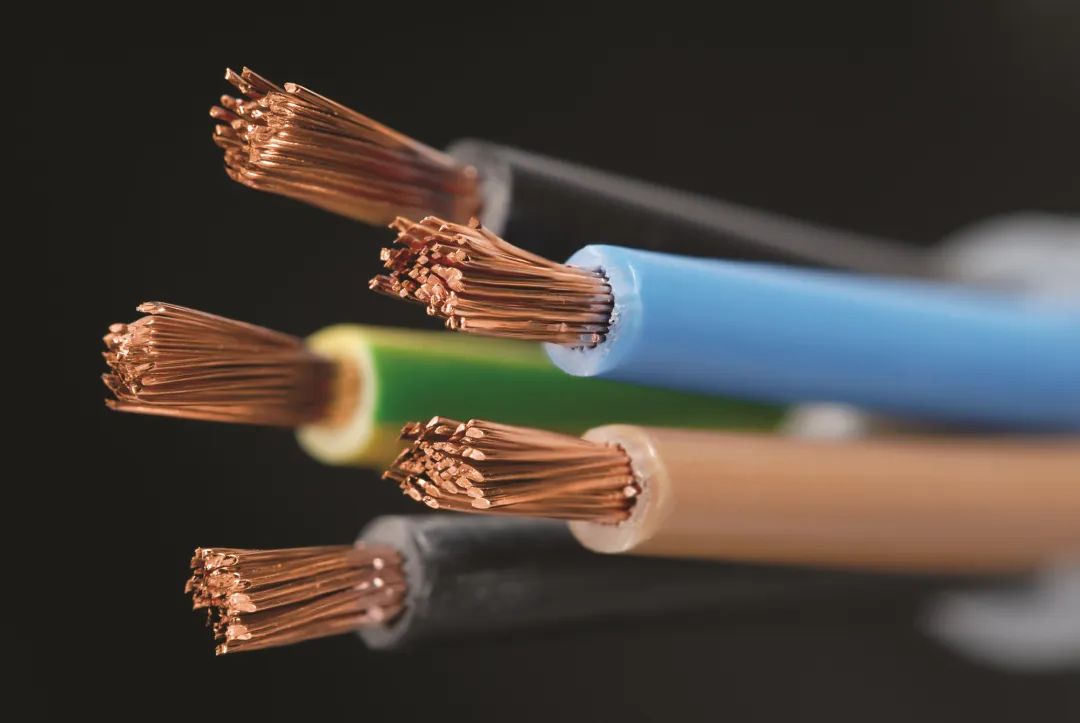
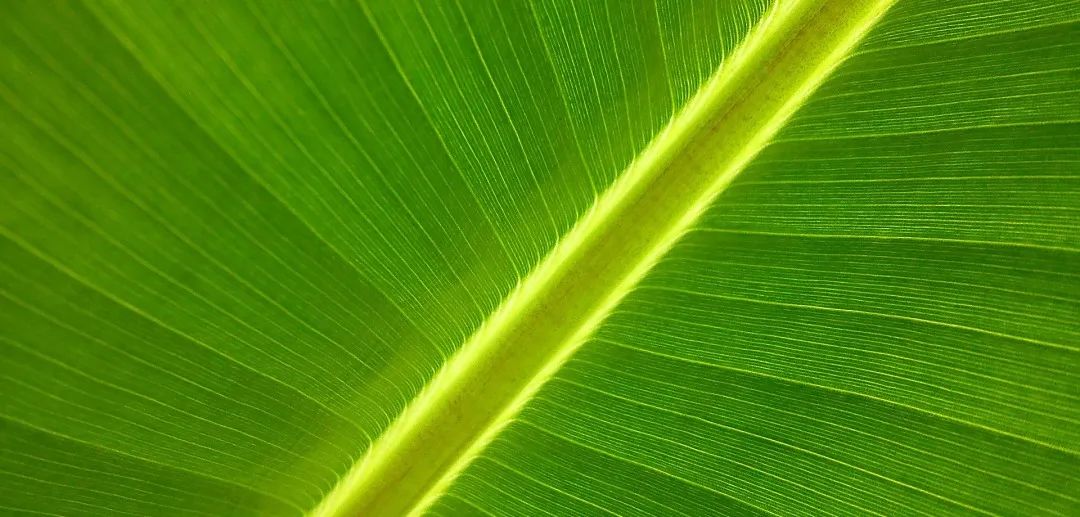
例如在纯电动新能源汽车中,电源电压一般在300 V以上、电流可以达到500 A,因此需要高压线束具有更高的耐温等级,一般在-40 ℃~125 ℃,部分需要达到150 ℃;其次要求高压线束的允许工作温升不超过55 K,以确保在大电流工作时,温度稳定在安全范围之内;此外,高压线束的线径大,工作电流达到500 A时,单芯导线线径需要达到135 mm2,而更粗的线束会造成弯曲应力变大,线束安装时,接插件插拔力也会增大。如果高压线束材料具有一定的柔性,将有助于抵消弯曲应力,提升线束与接插件连接的可靠性;同时,为了保证防水与漏电安全,连接器要求的防护等级大于IP67,而且为了防止大电流产生的电磁干扰,高压线束还有电磁屏蔽要求,一般要求铜丝编织屏蔽的覆盖密度≥85%,其编织铜线直径Ø>0.1 mm。
需要注意的是,随着800V系统的日渐普及,高压线束的技术要求也将进一步提升,对于整车线束布置带来新的挑战。首先需要面对的挑战是高压线束采用更大截面会带来布线的困难,一般要求高压线束的拐弯半径应大于高压线束直径的6倍以上;其次,高压线束的布置需要考虑电磁兼容性(EMC)、干扰源,高压连接线束建议远离易干扰部件及其连接线束,最好可以单独布置。高压线束与易干扰部件的连接线束的距离应超过10 cm,同时,将线束布置在金属车身的凹槽、夹角,或者紧贴金属车身布置可以有效降低电磁干扰。
综上所述,随着新能源汽车高压线束技术要求的提升,如何控制高压线束的工作温升,在满足载流量条件下尽可能减小线束截面积,这对于高压线束在新能源汽车中的安全使用和车内空间的布置具有重要意义。而为了满足高压线束的工作温升和优化线束布置,就不得不考虑高压线束的材料选择。
现阶段车用高压线束主要采用铜材料作为导体(参见QC/T1037-2016),包括裸圆铜线和镀锡软圆铜线绞合而成。铜材料具有优良的导电性能(20 ℃环境下,铜的电阻为0.0185 Ωmm2/m,铝的电阻为0.0294 Ωmm2/m)。在大电流情况下,其工作温升更低,一方面可以减少输电时发热损失,另一方面铜材料优良的导热性能也确保了高压线束的工作温度稳定在安全范围之内。同时,由于导电性优良,在相同载荷下,铜导线的截面积可以更小,这可以有效帮助高压线束的灵活布置,包括更小的拐弯半径(高压线束的拐弯半径一般需要超过线束直径的5~6倍以上);此外,更细的线束可以降低弯曲应力,安装线束时,接插件插拔力较小,帮助降低安装维护的难度,提高装配的稳定性和可靠性;而且,更小的截面积可以帮助高压线束灵活布置于贴合金属车身的凹槽、夹角,或者紧贴金属车身布置以有效降低电磁干扰。
☆ 除了良好的导电性能,铜材料作为高压线束导体材料的另一个优势是较好的拉伸强度与弯曲性能。金属铜具有较好的力学性能,抗拉强度为200-240 MN/M2,伸长率可达50%,其良好的塑性使其易于加工,具有很高的塑性变形能力,可采用压延、挤压和拉伸等压力加工方法制成各种形状和尺寸的制品,而用铜材料作为导体的高压线束在使用过程中可以承受车辆行驶过程中发生的振动与摩擦,具有较高的可靠性和更长的使用寿命。
☆ 铜材料还具有较好的化学稳定性,抗腐蚀性好,且易于焊接。车辆的运行环境复杂恶劣,高压线束和端子接头不可避免会工作在潮湿、盐雾等易腐蚀环境中。而根据传统汽车线束的使用经验,在潮湿、高温和振动的环境下,如与其他部件发生摩擦和碰撞,容易出现绝缘体磨损、接头松动、导线腐蚀等现象,进而导致断路或短路等故障的发生。由于高压线束承载更高的电压、更大的电流,并在端子和连接器上具有更大的应力,所以安全要求更高,需要导体材料具有更好的化学稳定性。高品质的铜材料既能确保端子和连接器长期保持良好的接触,避免电化学腐蚀的发生,也能减缓绝缘层老化或受损后,线束导体受腐蚀的影响。而该领域也是其他材料作为高压线束导体需要进行全面研究验证的主要难点之一。
简而言之,高压线束作为新能源汽车的血管与神经系统,对于新能源汽车具有牵一发而动全身的影响作用。高压线束的安全性是新能源汽车整车安全性的基础保障,其技术发展对于新能源汽车整车性能的提升具有重要作用。