如果单独把整车中电驱系统拿出来分析,电机成本在电驱系统中占 27%,控制器占比 60%,减速机构占比 13%。由此可见,电机和控制器成本占比较大,这两块是降本的大头,减速器虽然成本占比较小,但其配合的好的话,将事半功倍。
本文主要从电机定转子总成的制造工艺来谈一谈。
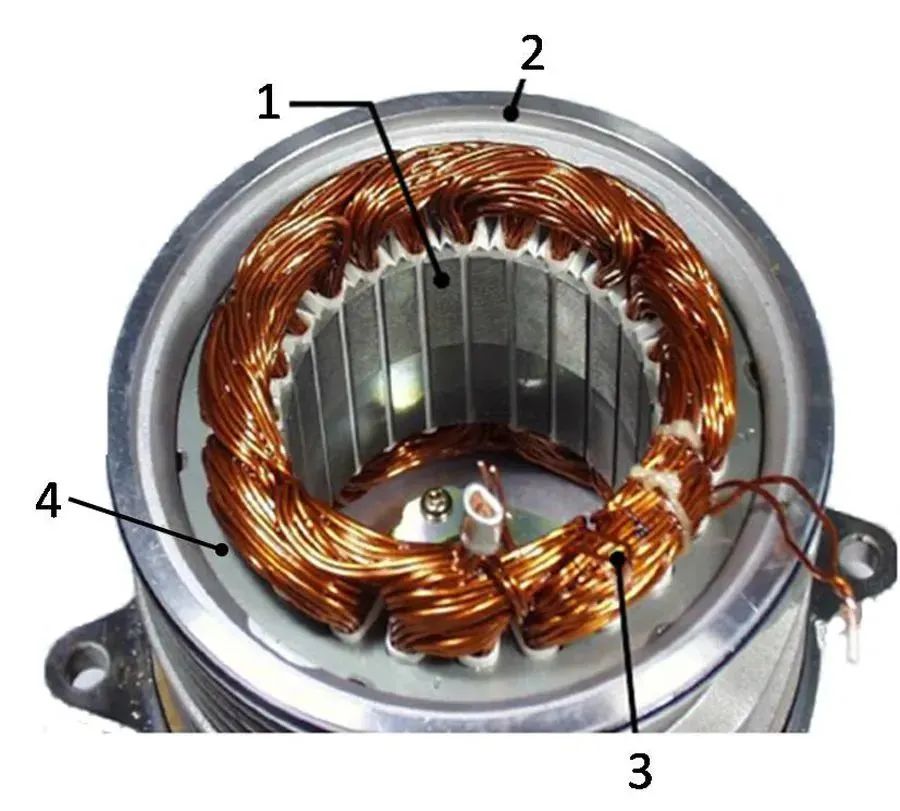
1-齿极 2-机壳 3-线圈 4-铁芯
据统计,定子总成约占永磁电机成本的35%。再者,新能源汽车个性化定制需求愈来愈大,多数车型处于中小批量状态,配装的永磁电机呈现结构多变、性能宽泛、订单急切及定子直径不等(80-400mm)的小众化现象。
由此,高成本的定子总成生产不可继续沿用传统制造方案,而是采用发卡技术、数字技术和信息技术等手段,提高定子产线的柔性度、集成度与高效率,进而减少空间占用、缩短交付周期及降低生产成本。
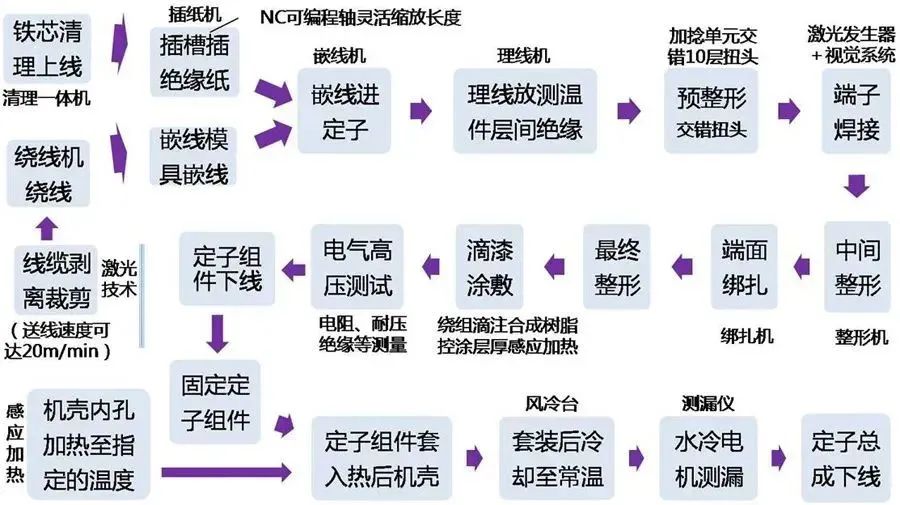
所用装备涉及工控性质的清理机、嵌线机、理线机、绑扎机等,也有激光技术的裁剪机、焊接机,还有伺服轴定位的插纸机、加热机、整形机和套装机,更有易燃易爆的浸漆、烘干设备,如图3所示。
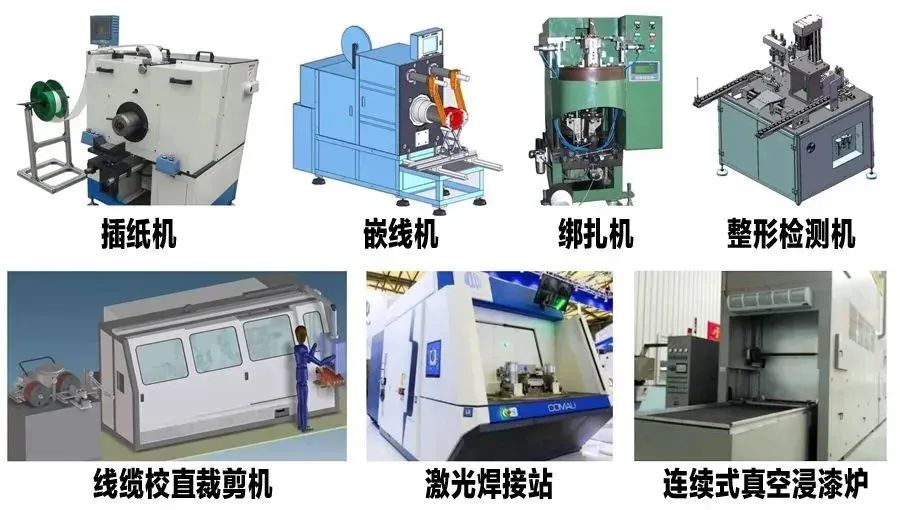
作业设备多、投资数额大、工序流转长、占地面积广、产品切换慢、机壳薄壁减材加工,这些是定子总成制造路线的显著特点。
在瞬息万变的个性化市场时代,电机制造商应:
- 采用机器人装卸料替代大量人工吊装;
- 采用AGV小车或悬挂链输送定子件;
- 采用数字化装备提高换型柔度;
- 采用互联网进行零件信息、产线状态、在线实控、订单分发等数据采集分析;
- 采用液/气压自定心快换多工位夹具(见图4)进行减材件的快速夹松;
- 采用云平台进行元器件供货商的最优协同派单等方法,
以此实现定子制造的降本控制,短期内快速换型完成小批量电机的制造,表面粗糙度和圆度分别不超过Ra1.6μm与8μm。
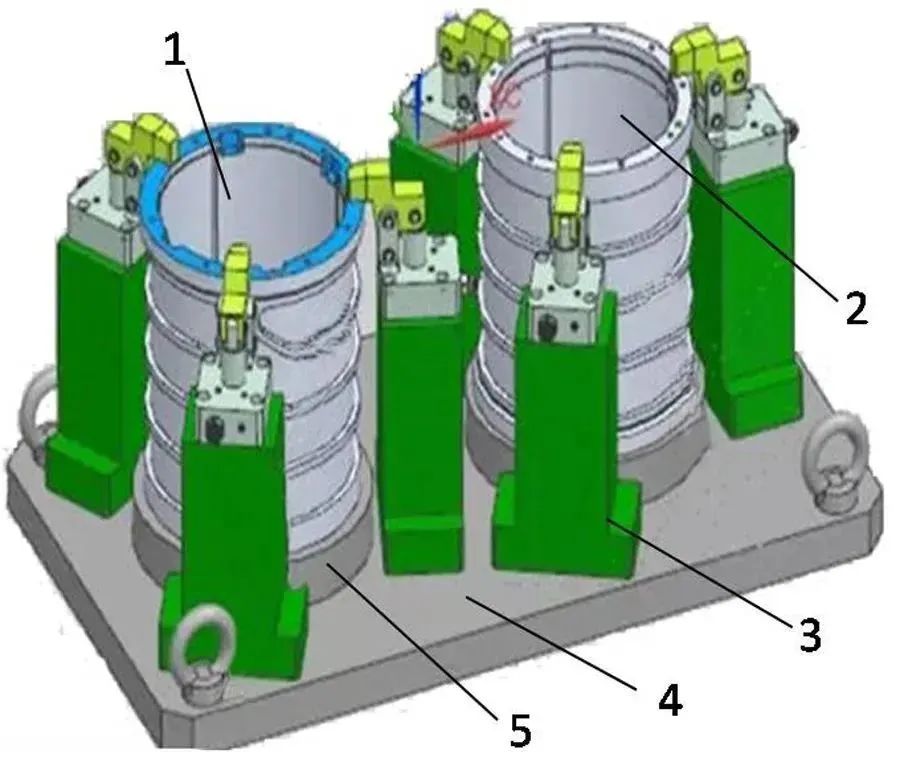
快换多工位夹具示意
1、2-电机壳 3-夹松结构 4-夹具底座 5-定位支承
这类电机的转子总成主要由转子轴、转子铁芯、永磁体(又称磁钢)及其前后挡板等件构成,如图5所示。
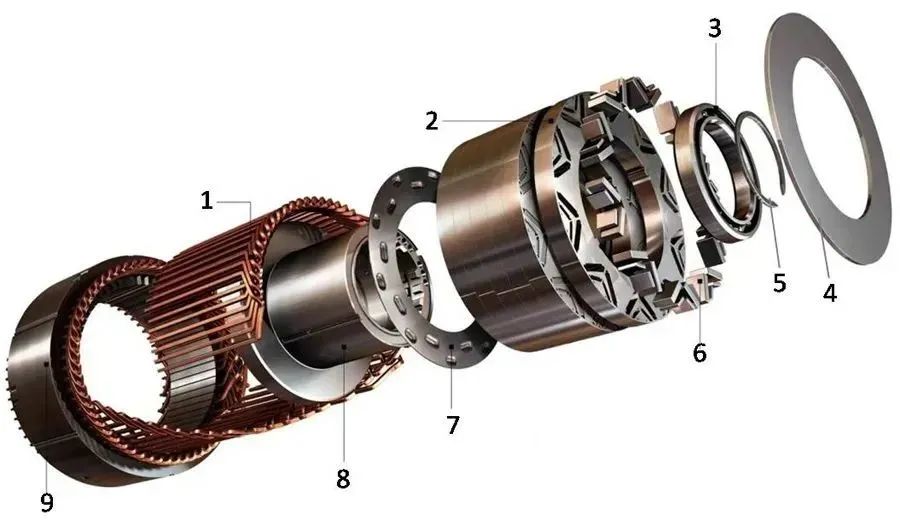
1-发卡定子线圈 2-转子铁芯截面 3-轴承
4-永磁体前挡板 5-止动垫圈 6-永磁体
7-永磁体后挡板 8-转子轴 9-定子铁芯
不同厂商的IPMSynRM在技术上各不相同,主要是永磁体的尺寸、位置、形状和数量等方面的差异。
从原理、设计到制作的每一环节,任意一个小变化,特斯拉、BBA、丰田、本田等厂商均会进行多频次的软件仿真和硬件测试,形成独有的核心知识产权。
菲索玛特Felsomat公司采用模块化的智能制造集成化方案,创新转子设计,通过软件获取铁芯的合成磁场图,改善铁芯角度和永磁形式,优化工艺路线,进行数字化切削、自动化装配及数据化分析,使电机转子经内置永磁和V形开槽对应产生永磁转矩与磁阻转矩,最终实现电机低速的最大转矩角和高速工况的弱磁。
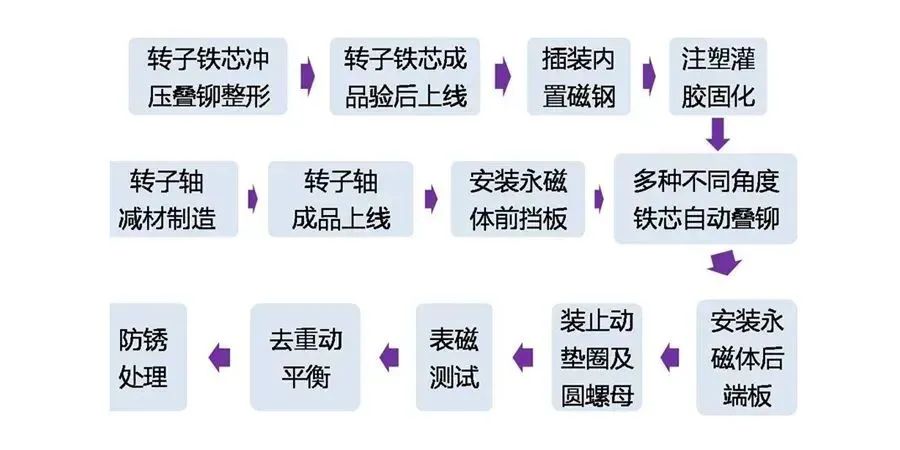
表磁测试涉及磁极数、极性、磁极峰值、角度、面积、宽度和半宽高等参数检测。
其中,钕铁硼等稀土材料的永磁体成本约占总成本的44.9%,钢材和铜绕组结合的定子铁芯成本占17.4%,镁铝合金材质机壳和钢质转子的成本分别占12.8%与7.5%。
一旦原材料价格上浮和用工成本增大,永磁电机成本势必增加,新能源汽车售价必会随之浮动。
因此,国内电机供应商可借鉴欧美、日韩企业电机降本的有效措施,使电机产品具有集成化、轻量化、个性化的耐用、低价、安全特点,从而使电驱动系的峰值功率密度和连续功率密度可在2020年4kW/kg与2.2kW/kg的基础上连续倍增。
这些措施包括:
- 转子轴和支承零件等采用耐磨非金属材料替代,以降低系统总重和成本;
- 探索应用新型材料,如覆盖巴克明斯特富勒烯分子的钴薄膜,以解决稀土资源的匮乏及开采中的毒副作用和环境破坏问题;
- 通过优化电机结构,如极槽比、齿槽比、裂比等,提高材料利用率;
- 重置工艺路线,去库存,优流程,省资源,除内耗,提效益;
- 引入金属3D打印,取代流程长、设备多、固资大的生产线;
- 加大自动装配和柔性切削覆盖度,在磁钢插装、零件装卸、表磁测试、塑胶固化等环节全部采取机器人操作,转子轴、挡板、垫圈、端盖和变速器底壳等件的加工在自动化产线上完成(见图7),通过减少残次废品和提高班产量来降低单件成本等。
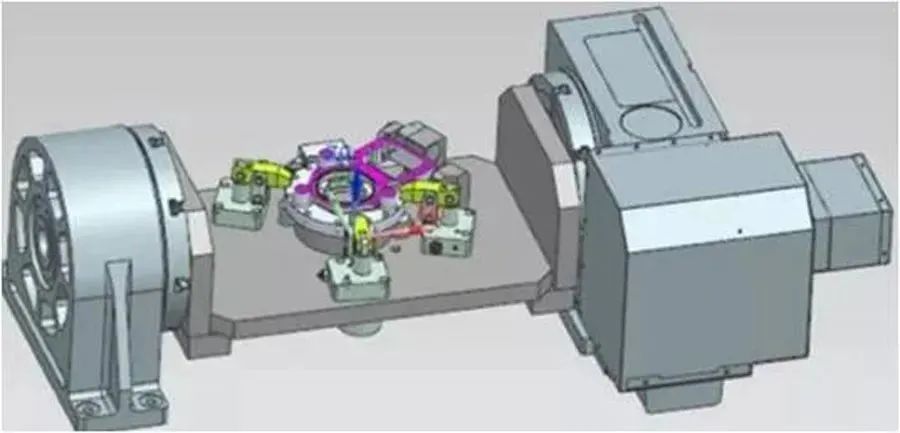
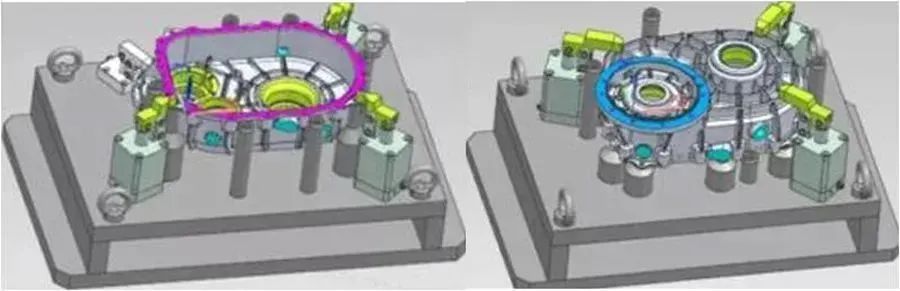
图7 柔性切削下电机端盖和变速器底壳的快速装夹示意
通过生产设备网络化搭建车间物联网、生产数据可视化进行生产决策、生产文档无纸化助力高效绿色制造、生产过程透明化实现中枢神经总控、生产现场无人化提高产量和质量,FANUC公司实现了月生产伺服电机18万台、销售额占世界市场50%、日本国内市场70%的业绩突破。
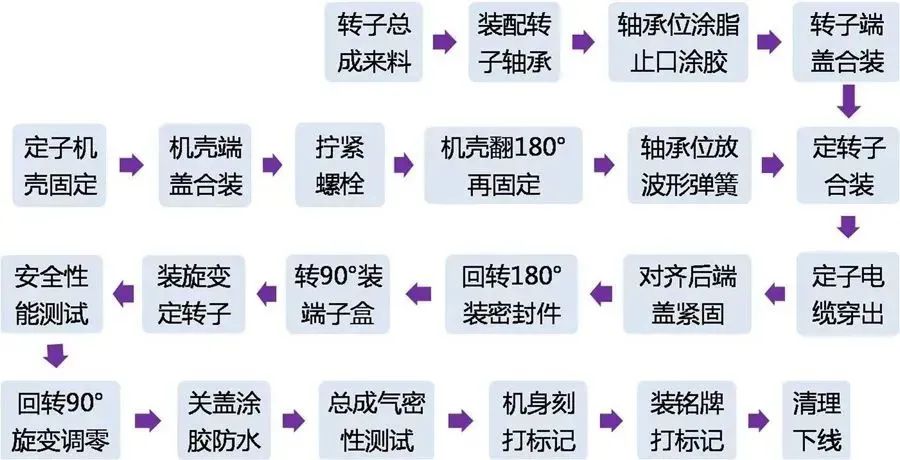
建议国内电机供应商参考借鉴FANUC公司建厂、建线经验,吸收其在效率发挥、业务拓展、人事优化、财务管理等方面的精髓,打造定转子合装测试(见图8)无人车间,通过深度学习、网络搭建、聚智创新、协同配售、精准营销等手段,实现永磁电机基于操作智能、运营智能和商业智能三个层次的全流程化经销,从而在阔步腾飞的新能源汽车市场上分得一杯羹。
目前,比亚迪、长安、广汽埃安等OEM官宣正在应用或即将量产多合一电驱总成,华为、巨一动力、威迈斯、智新科技等电驱供应商均展现了多合一开发或配套进程。
上下游企业皆认同,动力总成的深度集成化技术将经历三大阶段:
- 物理集成;
- 动力域深度集成;
- 多域高度集成。随着集成化程度的提升,将持续地激发出降本增效的潜力。
其中,巨一动力通过多合一电驱产品平台开发项目和实车测试,真正体现了降本增效效果。
物理集成阶段的技术方案是基于六合一的主从分布架构,依据现有平台的零部件共用策略,电机与电控、减速器共壳体,减少连接线缆和冷却水管。MCU、DCDC、OBC、PDU等控制器可根据功用集成为逆变砖、电源砖、配电砖等平台化子系统,共享线束、连接器、壳体,降低硬件成本,且通过平台化设计适配不同级别的整车,降低开发成本,缩短开发周期。
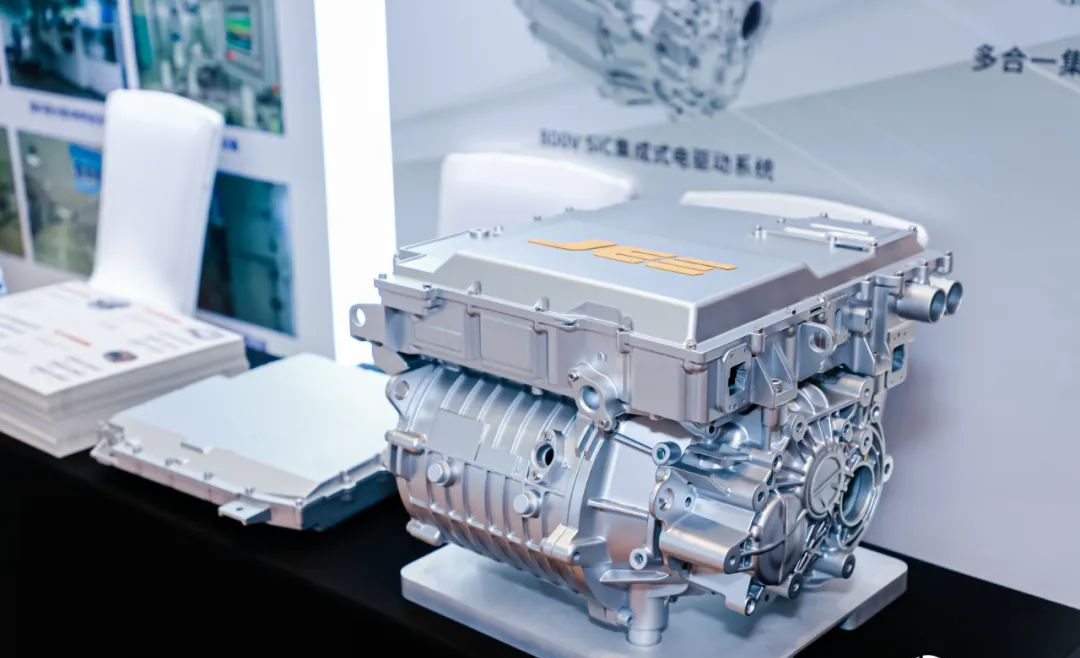
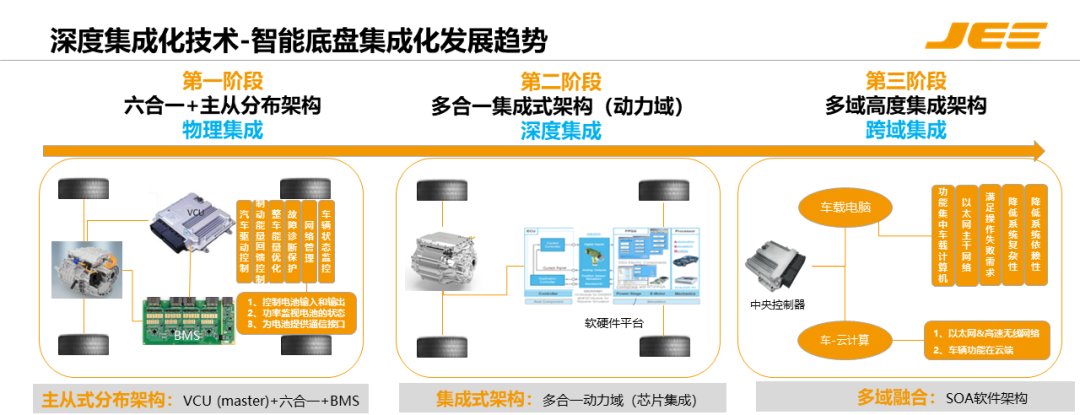
目前巨一动力的多合一电驱总成已迈过第一阶段,走向第二阶段的终极方向。经高度集成,其多合一方案能够大幅降低成本,使重量、体积缩减10%~20%,提升系统高效区面积,降低NVH噪音。
同时,比亚迪、长安、威迈斯等电驱上下游企业表示,共享硬软件资源降本之外,多合一方案还能够简化开发周期,降低开发成本,提升驾乘体验。
综合主流OEM和电驱供应商的方案和思路,多合一的降本增效主要是通过两大方面来实现:
- 多合一方案通过共享壳体、线束、连接器等硬件,融合电子电路和软件算法,实现BOM降本。
- 多合一方案可以简化OEM供应链的管理,缩短开发周期,实现高效管理降本。
金田铜业生产铜棒、铜带、铜排、铜板、铜线、电磁线、磁钢等,欢迎来电咨询,联系电话:0574-83005999,微信:18057437999。