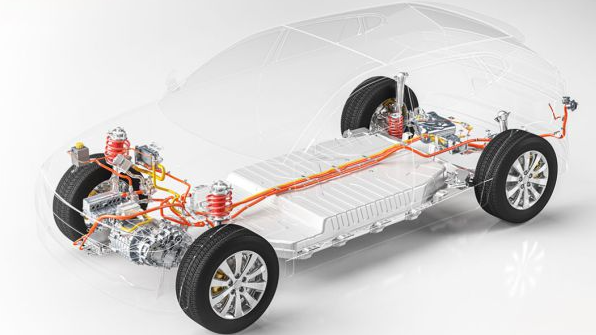
| 1 高压线束布置的一般原则
电动车的高压线束布置需要基于就近原则,使用尽可能少的高压电缆来完成走向布置,这个大原则即满足了总布置和高压电气设计需求,也满足整车降本增效和减重的目的。
正常情况下,可以将高压线束布置分为两种情况:分层布置和并列布置。
1.1 分层布置
高压线束与低压线束分为上下层级关系。
为了避免高压线束传输强电电流时产生电磁干扰,导致低压线束对控制单元供电及信号传输受到电磁干扰的风险,一般采用高压线束与低压线束分层设计;
由于不同车型电流大小不同,一般高低压线分层之间距离保证在200-300mm内。
考虑不同车型电流大小不一样,商用车高低压平行走线距离间隔须大于400mm,乘用车高低压平行走线距离间隔须大于200mm;若实际情况不满足此距离,可考虑相互垂直走线。
经实车验证,该方案有效避免了强电工作时产生的干扰。分层布线可以有效对高压线工作时产生的EMC干扰起到防护作用。
1.2 并列布置
走向相同但采用依附车身机构并列布置。
采用并列式布置,保证高低压线束并列不交叉。有效防护高压线束工作时对控制器的EMC干扰。
并列式布线方案适用于混合动力车型,将高压线束连接单元布线区域和发动机电喷线束布置区域并列。进而有效避免高压线束传输供电时产生的电磁干扰。
2 高压线束布置要点——安全相关
高压线束具有远高于传统低压导线的重要特性和较高的防护等级。高压线束的布置除了要满足目测隐蔽、安全碰撞法规、人机工程及维修方便性外,还需要制定针对高压电的有效防护措施,高压线束的不合理布置可能导致漏电,引起火灾,危及驾乘人员安全。
2.1安全布置原则
高压线束安全布置的第一原则——防止驾乘人员或维修人员可直接接触到高压线束。
基于此原则,乘客舱禁止布置高压线束,行李舱应避免布置高压线束。
如因设计需要,确实需要在上述区域内布置高压线束,则应结合碰撞安全、高压安全、零件使用安全等方面的考量,通过车身钣金过孔,使高压线束在车辆底盘下布置,且必须有覆盖物遮盖,避免人员误触。
2.2 避让挤压和振动幅度过大的区域。
高压线束在布置时,还需要注意避让挤压和振动幅度过大的区域。
2.2.1 避让挤压区域
对于诸如翼子板区域、汽车千斤顶或其他起重工具支撑区域等容易与其他部件发生挤压的区域,均应避免布置高压线束。
由于车辆工作工况复杂,极端情况下会出现车身碰撞受压变形的情况。
作为承载新能源车型动力源传输功能的高压线束,在布置时,应将避免受车身变形影响考虑在内,尽可能避免或减少高压线束受车身变形影响而导致破损漏电的情况出现。
高压线束应尽量避免布置在诸如前后防撞梁、侧围钣金和前舱车头等车辆碰撞后会发生较大变形的区域。
当电动汽车发生碰撞时,需要考虑高压电气连接处在车身吸能形变时的位移路径,避免因车辆碰撞,导致高压线束直接被钣金割裂或金属残片刺破绝缘层进入导线线芯内部造成高压短路,对驾乘人员造成电击伤害。
要求在没有碰撞侦测的碰撞中,等电势功能必须保持生效。
2.2.2 避让振动区域
高压线束在布置和固定时,应避开剧烈振动区域。高压线束应与其连接的高压设备连接无相对振动。
如无法避让振动区域,则应根据线束布置部位的振动幅度、运动件的最大运动包络,留有足够的高压导线余量,避免让线束承受拉力或者张力。
行驶车辆在长期颠簸状态下,容易引起高压线束固定点位置错动、脱落,进而导致两固定点间的距离瞬间增大,拉扯线束致使内部节点拉脱或虚接,因此高压导线长度控制要合理,长度既要留有富余,以抵消运动拖曳带来的应力,又要避免过长导致线束扭曲。
若高压线束确实需要在振动区域固定,布置建议如下:
1) 第一个固定点距离导线出口处最大100mm;
2) 第一个固定点所用的固定件必须直接安装在导线上或安装在套管上(避免布置在波纹管上);
3) 固定点对高压导线施加的压力不可对导线的绝缘电阻产生影响。
2.3 与油管/制动管等管理间隙要求
在布置高压线束时,应避免高压线束与燃油管道和刹车油管交错布置,即使在平行布置时,高压线束和油管之间的距离也应大于100mm。
2.4 高压线束弯曲半径
不论是避让挤压,还是避免振动幅度过大区域,高压线束在布置时,需要注意其弯曲半径。这是因为高压线束的弯曲半径对于高压线束的电阻影响很大,若高压线束被过分弯曲,线束折弯部分的电阻变大,将造成线路压降增大。
高压线束具有较大的外径和重量,为避免应力的集中,
在静态负载下,高压导线最小的内弯曲半径不应小于四倍的导线外直径。
在动态负载下,高压导线最小的内弯曲半径不应小于八倍的导线外直径。
需要避免在接头中存在弯曲导线,否则接头后部密封件里可能出现漏电通路。
高压连接器尾部出线的高压线束需保持直式出线,靠近连接器尾部的高压导线不得弯曲受力,不得旋转。
3 高压线束布置要点——EMC相关
由于高压线束存在电磁干扰低压用电器和低压线束的可能,因此,对于高压导线以及和其对配的接插件连接处需要360°的屏蔽围绕保护。
对于高压线束中的每根导线,需要确保其从一端的接插件到另一端的接插件的屏蔽层电阻最大为26毫欧(对于三相线束中的每一根导线,应确保其从一端的接插件到另一端接插件的屏蔽层的电阻最大为11毫欧)
屏蔽层的电阻值要求限定了高压线束布线时的导线长度。
为了能够更好的提高整车电磁兼容性,在进行高压线束铺设设计时,一般建议遵循以下布置原则:
(1) 干扰源及其连接线束(一般为高压线束),建议远离易干扰部件及其连接线束(一般为低压线束,特指低压线束中的信号线),尽可能单独布置。
(2) 当高低压线束平行布置(同向走线)的长度大于200mm时,高低压线束之间的间距建议至少为100mm,防止高压线束产生的磁场对易干扰部件造成影响。
(3) 高压线束导通高压电时,会在周围形成强磁场,因此高压回路的负载和电源之间的布置距离应尽可能短,同时将高压线束靠近车身金属钣金布置,从而减小回路面积,降低磁场的对外辐射量。
高压导线产生的强磁场 示意图
(4) 属于同一整体的配套的高压线束(比如电机的三相线束)必须共同对称地布置在一起。
(5)属于同一整体的配套的每两根高压线束间距建议不得超过20mm,单根导线长度差建议不得超过35mm。
4. 高压线束布置要点-密封防水
为了提高高压线束的机械防护和防尘防水性能,在接插的连接器间以及连接器连接电缆的位置均采用密封圈等防护措施,防止水汽和灰尘进入,从而确保连接器的密封环境,避免接触件之间短路的风险,以及防止湿气进入,避免产生火花等安全问题。
对于布置在发动机舱及底盘部分的高压线束应特别注意线束的保护方式。
布置在底盘部分的高压线束应充分考虑车辆涉水、刮底盘等情况, 在布置设计高压线束的时候充分考虑防水、防泥沙飞溅、防刮伤等因素,可以采用塑料线槽、金属弯管设计来保护高压线束。线槽考虑可装配性,分槽盖导槽将高压线束扣合后固定在车底板上,金属弯管工艺较复杂,便于安装。
目前大多数高压线束采用包覆物对高压线束进行保护,包覆物的作用主要有防磨、降噪、隔辐射热源、美观等,一般选用橙色耐高温阻燃波纹管或者橙色耐高温阻燃布基袖套完全包覆。
对于安装在车辆底部、轮舱溅水区的高压线束,需要特别注意水和道路磨料对导线/连接器的损伤。其中安装在车辆涉水线下方的高压导线,应全部采用密封/防水措施。
密封防水主要从线束零件选型和线束布置两方面共同作用。
4.1 密封措施
高压导线与高压连接器匹配,采用导线密封件、热缩管、橡胶件等多种方式进行密封,以达到IP67等级的防水防尘要求。
各类密封措施 示例
4.2 防水布置
4.2.1 设置滴水点
高压导线从连接器接口处出来后,在允许出现高于连接器中心水平面进行布置之前,必须设置滴水点,先保证有一段高压线处于连接器中心水平面之下,以保证雨水不会沿着高压线束倒流进高压零部件内部,如下图所示。
图 303 防水布置示例
4.2.2 设置正确的连接器方向
高压连接器的布置位置和方向也同样需要注意,为了避免高压连接器尾部凹陷结构积水,连接器应避免尾部向上、垂直布置,尽量选择尾部朝下或水平布置。
4.3 耐热要求
高压线束的布置还需要注意耐热要求。
高压线束应远离热源,与热源(如发动机排气管等高热部件)的距离至少大于200mm。
如因客观原因无法满足该距离要求,那么需要采用诸如阻燃隔热棉或者可以反射热能的罩盖对线束进行包扎或覆盖,以抵抗辐射热源。
5. 高压线束布置要点-线束固定与防护
高压线束的固定方式多种多样,可依据整车不同区域的情况,合理选用不同固定用零件,在布置时,一般遵循以下规则:
5.1 绝缘性能
不论何种固定/防护用零件(避免使用铁件),都应具有绝缘性能,并得到充分保护,防止其腐蚀生锈,从而影响其固定可靠度。
5.2 固定件布置距离
为减小高压线束摆动对连接器或压接端子产生影响,高压线束在布置时,需在连接器尾部出线不大于120mm处进行首次固定。
高压线束若无法铺设在导线槽中,则需要每间隔150mm至250mm进行固定。
当高压线束沿直线铺设时,两个相邻固定点间隙应满足如下要求:
(1) 高压线束截面积>16mm²,相邻固定点间隙≤300mm;
(2) 高压线束截面积≤16mm²,相邻固定点间隙≤200mm。
当高压线束受环境影响,需要安装在活动件(诸如皮带、风扇、传动轴等)附近,且必须以弯曲的状态进行固定时,则需要合理分布载荷,一般建议增加可以长期承受较大作用力的辅助固定件用于固定,相邻的两个固定件间距≤300mm,且在过弯的两个端点固定,固定点与连接器间距应≤150mm,才能够在承受线束的重量和振动载荷的前提下,即不造成线束磨损,也不对附近的活动部件造成干扰。
高压线束不得对活动件造成干扰,两者之间距离不得小于50mm。
5.3 高压线束固定方案
高压线束通常沿车身钣金布置和固定, 车辆在运行过程中,无法避免会产生振动,因此所有高压线束都需要做好固定。各类固定件使高压线束与车体之间的相对运动尽可能小,并同时对高压线束起到固定、保护和导向的作用。
高压线束由于强度大,根据线束的长短不同需要进行不同的处理,一般要求用光滑无毛刺的支架、线槽、线夹、扎带等进行固定;用扎带固定时,应充分考虑固定方式,以便于选择合适的扎带进行固定,避免固定失效风险。有线束卡扣扎带的选型设计,规范等要求,请在线束工程师之家网搜索“扎带”关键词找。
目前,高压线束常见的紧固方式包括如下几个方案:
(1) 圆孔方式固定,通常使用一体式固定扎带附楔形固定头、一体式固定扎带附杉树形固定头。
(2) 焊接螺柱固定,通常使用一体式焊接螺柱固定扎带、带焊接螺柱固定件隔离式双夹头扎带。
(3) 管道式固定,使用扎带和管夹类卡扣组件套箍高压线束外侧进行固定。
(4)板材边缘固定,针对边缘不超过3mm的金属板材,使用边缘卡扣进行固定。
(5) 导线支架固定,对于线径≥35mm²的高压导线,一般使用导线支架间高压导线上抬,使其与车身突出部分拉开距离,防止高压导线磨损。
(6) 连接器固定,指的是安装在高压连接器上的固定件,该固定件一般有额外的固定头可插入车身钣金孔,将连接器固定在车身或高压设备上。
5.3 高压线束防护方案
高压线束安装布置区域附近存在金属部件,会有毛刺、凸缘等结构,需要使用防护零件进行保护,减少高压线束磨损的可能。
线束在车内外走线时环境较为复杂,需要根据其在车辆上的布置位置以及使用工况,在其外表面用橙色波纹管、编织物管、胶带或是其他外敷物进行包裹,以增加其耐磨性、隔热性以及美观性,使高压线束能在不同环境下正常使用。
常用的线束外敷物包括波纹管、护套、护套及胶带等,起到防磨、隔热、减震和警示等作用。
5.3.1 波纹管/袖套/套管防护
纯电动汽车动力电池布置在车辆后方下底板中,电池前端引出的高压线束从车辆底板下面经过,离地面较近,需在线缆外部增加波纹管防护,以防止在行车过程中高压线束遭受到路面飞溅的石击等。
没有特殊要求,高压线束可采用波纹管进行包覆。
闭口式波纹管的特点具有耐磨、阻燃、耐热等特点,波纹管的耐温范围在-40℃~150℃,短时间还能达到200℃。
5.3.2 护板/导线槽防护
部分位置因为空间的需求,线束无法应用波纹管进行防护,可以考虑在高压线束外增加塑料线槽的方案来对线束进行防护。
护板/导线槽通常被使用在环境较为恶劣严苛的区域。例如,布置在车辆底盘下防的高压线束,考虑其可能遭受的浸水、车辆剐蹭及泥沙飞溅,需要使用护板/导向槽进行防护。
护板和导线槽除了能起到固定和保护线束的作用,还能起到导向的作用。当遇到折弯空间有限,需要高压线束按照特定走线进行布置的情况时,即可使用护板/导线槽对线束进行固定和导向。
对于需要在某些特殊区域布置的高压线束,还可以采用线束护管进行遮挡与防护。一般护管/护板都具有化学性能稳定,不老化,耐腐蚀力强等特点。
护板和导线槽多用金属或塑料制成,具有高抗冲、高耐热,低温时具备高冲击强度,耐燃性。
对于安装在车辆底盘下的护板,还需额外通过耐石子冲击测试。
目前有部分高压线束供应商将护板/导向槽和高压线束做成一体式,减少主机厂总装车间的装配工序,提高装车效率。
5.3.4 套管防护
对于易损伤易受冲击的部位可以采用套管,可以有效起到防止线束磨损的作用,其特点是耐高温、防冲击、防切割、轻巧以及易于安装,与波纹管相比,其耐磨性更高,外径更小,当成本会有所提高。
套管的选型颜色与波纹管相同,应为橙色。
套管有开口自卷和闭口之分,开口自卷型安装较方便。当使用开口自卷护套时,卷边的重合率需到达30%。
5.3.5 耐磨胶带防护
相比于波纹管和套管,胶带用处更为广泛和方便,常用于保护、捆扎、阻燃、标记等作用。使用胶带包括的高压导线,增加的线束外径尺寸最小,几乎不对外观尺寸造成影响。
5.3.6 橡胶件防护
高压线束要避免从尖锐物、金属架边缘、焊接缝、车身上的固定孔处走线,避免因装配操作、振动摩擦使得高压线束外敷物磨破,导致线束损伤而造成安全事故。
如无法避免锋利边缘或需要穿孔时,应在过孔等锋利边缘添加相应的防护装置(例如橡胶件、橡胶圈等),或在导线表面增加保护结构,防止高压线束在安装时遭到损坏。
高压橡胶件考虑强度问题,采用橡胶与塑料结合件,对钣金固定匹配、抗拉伸强度都有保证。
高压线束一般较粗,弯曲应力相对很大,高压连接器体积较大,在橡胶件设计上体积会大很多,同时固定强度要求也会很高,结构方面相对比较复杂,材料选择方面要求会更高。
根据结构、固定方式及安装位置的不同,汽车线束上使用的橡胶件类型也不同。有线束橡胶件的选型设计,橡胶件的规范,实验等要求可以在线束工程师之家网搜索“橡胶件”关键词找到。
根据橡胶件结构的不同可分为有骨架和无骨架两种类型;根据橡胶件固定方式的不同可分为单孔固定和双孔固定两种类型。
不同外形和密封构造的橡胶件 示意
6. 高压线束布置要点——安装便利性
在进行高压线束布置时,还需要同时考虑整车装配过程中,以及售后返修过程的便利和可操作性。
因此高压线束尤其是高压连接器的布置方案,要在诸多限制条件下找到合适的平衡的点。
一般所有连接器位置预留不小于200mm的空间,在安装时需要足够的手部操作空间,以便于连接和断开操作。连接器和部件之间的连接应该适当消除机械应力。
这项工作可在前期设计时,通过3D软件模拟仿真,以确认为每个连接器预留的空间是否具有实际操作性。
总体而言,在电动汽车上布置高压线束,应当遵循易于装配、易于维护和安全稳定的原则,结合电动汽车自身特点,合理规划高压线束布置,不断提高其合理性和可靠性。
金田铜业专注于铜加工领域30余年,生产铜棒、铜带、铜板、铜管、管件、铜线、电磁线、铜排、稀土钕铁硼等产品,在广东、江苏、重庆、越南、包头等地设立生产基地。